The Lawfulness of Digital Signatures for Logistics in Canada
- Quick to start
- Easy-to-use
- 24/7 support
Simplified document journeys for small teams and individuals
eSign from anywhere
Upload documents from your device or cloud and add your signature with ease: draw, upload, or type it on your mobile device or laptop.
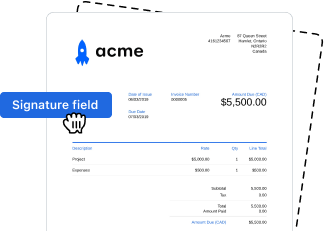
Prepare documents for sending
Drag and drop fillable fields on your document and assign them to recipients. Reduce document errors and delight clients with an intuitive signing process.
Secure signing is our priority
Secure your documents by setting two-factor signer authentication. View who made changes and when in your document with the court-admissible Audit Trail.
Collect signatures on the first try
Define a signing order, configure reminders for signers, and set your document’s expiration date. signNow will send you instant updates once your document is signed.
We spread the word about digital transformation
80%
completion rate of sent documents
80% completed
1h
average for a sent to signed document
20+
out-of-the-box integrations
96k
average number of signature invites sent in a week
28,9k
users in Education industry
2
clicks minimum to sign a document
14.3M
API calls a week
be ready to get more
Why choose airSlate SignNow
-
Free 7-day trial. Choose the plan you need and try it risk-free.
-
Honest pricing for full-featured plans. airSlate SignNow offers subscription plans with no overages or hidden fees at renewal.
-
Enterprise-grade security. airSlate SignNow helps you comply with global security standards.
Your complete how-to guide - digital signature lawfulness for logistics in canada
Digital Signature Lawfulness for Logistics in Canada
In Canada, the use of digital signatures in logistics is governed by specific laws to ensure their legality and validity. Understanding the legal aspects of digital signatures is crucial for businesses operating in the logistics industry in Canada.
airSlate SignNow Benefits
- Launch the airSlate SignNow web page in your browser.
- Sign up for a free trial or log in.
- Upload a document you want to sign or send for signing.
- Turn your document into a template for future use.
- Open the file and make necessary edits by adding fillable fields or required information.
- Sign the document and add signature fields for recipients.
- Click Continue to set up and send an eSignature invite.
airSlate SignNow empowers businesses with an easy-to-use, cost-effective solution for sending and eSigning documents. With great ROI, tailored for SMBs and Mid-Market, transparent pricing, and superior 24/7 support, airSlate SignNow is a top choice for businesses of all sizes.
Experience the benefits of airSlate SignNow and streamline your document eSign process today!
How it works
Select a PDF file and upload it
Add fillable fields and apply your eSignature
Send the document to recipients for signing
Rate your experience
Collect signatures
24x
faster
Reduce costs by
$30
per document
Save up to
40h
per employee / month
-
Best ROI. Our customers achieve an average 7x ROI within the first six months.
-
Scales with your use cases. From SMBs to mid-market, airSlate SignNow delivers results for businesses of all sizes.
-
Intuitive UI and API. Sign and send documents from your apps in minutes.
FAQs
-
What is the legal status of digital signatures for logistics in Canada?
In Canada, digital signature lawfulness for logistics is recognized under the Personal Information Protection and Electronic Documents Act (PIPEDA) and provincial legislation. This framework ensures that digital signatures hold the same legal weight as traditional handwritten signatures, making them a reliable option for logistics documentation.
-
How does airSlate SignNow ensure compliance with digital signature laws in Canada?
airSlate SignNow complies with the digital signature lawfulness for logistics in Canada by utilizing secure encryption and authentication processes. Our platform adheres to relevant legal standards, ensuring your documents are legally binding and acceptably compliant for Canadian businesses.
-
Are there any costs associated with using airSlate SignNow for digital signatures?
Yes, airSlate SignNow offers various subscription plans tailored to meet different business needs. Our pricing is competitive and designed to provide value while ensuring compliance with digital signature lawfulness for logistics in Canada, making it accessible for businesses of all sizes.
-
What features does airSlate SignNow offer for managing logistics documentation?
airSlate SignNow provides a robust set of features including customizable templates, automatic reminders, and real-time tracking of document status. These functionalities streamline your logistics processes while ensuring adherence to digital signature lawfulness for logistics in Canada.
-
Can I integrate airSlate SignNow with my existing logistics software?
Absolutely! airSlate SignNow supports various integrations with widely-used logistics software and applications. This capability enhances your workflow and maintains compliance with digital signature lawfulness for logistics in Canada, helping you to operate more efficiently.
-
What benefits does using digital signatures provide for logistics companies in Canada?
Utilizing digital signatures enhances efficiency, reduces paper waste, and minimizes turnaround times, especially critical in the fast-paced logistics sector. By ensuring digital signature lawfulness for logistics in Canada, companies can maintain compliance while enjoying the benefits of a modernized documentation process.
-
How secure are my documents when using airSlate SignNow for digital signatures?
Security is paramount at airSlate SignNow. We apply advanced encryption methods and adhere to best practices in cybersecurity, ensuring that your documents remain safe and meet the digital signature lawfulness for logistics in Canada.
Related searches to digital signature lawfulness for logistics in canada
Digital signature lawfulness for logistics in canada pdf
are digital signatures legal in canada
legal signature requirements canada
electronic signature canada
cra electronic signature requirements
electronic signatures ontario
electronic signature cra
pipeda electronic signature
be ready to get more